iSqFt Is Now Constructconnect
With the combined power of iSqFt and ConstructConnect you have access to the largest network, robust project data, and powerful takeoff and estimating tools.
Start searching projects bidding in your area now.
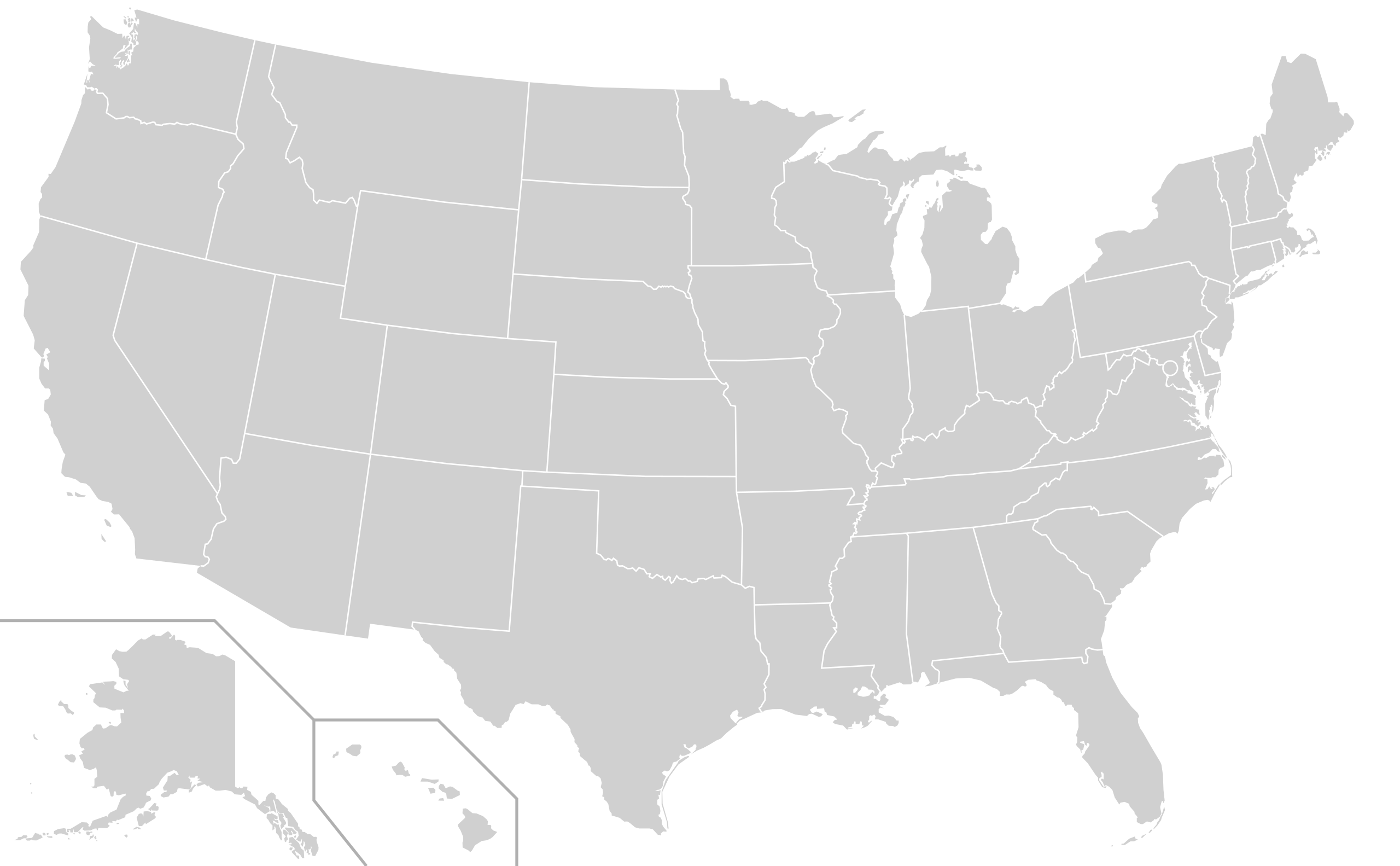
Privately Funded
Bidding Soon
Documents Available
Publicly Funded
Addenda Available
Post-Bid
Privately Funded
Bidding Soon
Documents Available
Publicly Funded
Addenda Available
Post-Bid
Privately Funded
Bidding Soon
Documents Available
Publicly Funded
Addenda Available
Post-Bid
Privately Funded
Bidding Soon
Documents Available
Publicly Funded
Addenda Available
Post-Bid
Privately Funded
Bidding Soon
Documents Available
Publicly Funded
Addenda Available
Post-Bid
Privately Funded
Bidding Soon
Documents Available
Publicly Funded
Addenda Available
Post-Bid
Privately Funded
Bidding Soon
Documents Available
Publicly Funded
Addenda Available
Post-Bid
Privately Funded
Bidding Soon
Documents Available
Publicly Funded
Addenda Available
Post-Bid
Privately Funded
Bidding Soon
Documents Available
Publicly Funded
Addenda Available
Post-Bid
Privately Funded
Bidding Soon
Documents Available
Publicly Funded
Addenda Available
Post-Bid
Privately Funded
Bidding Soon
Documents Available
Publicly Funded
Addenda Available
Post-Bid
Privately Funded
Bidding Soon
Documents Available
Publicly Funded
Addenda Available
Post-Bid
Privately Funded
Bidding Soon
Documents Available
Publicly Funded
Addenda Available
Post-Bid
Privately Funded
Bidding Soon
Documents Available
Publicly Funded
Addenda Available
Post-Bid
Privately Funded
Bidding Soon
Documents Available
Publicly Funded
Addenda Available
Post-Bid
Privately Funded
Bidding Soon
Documents Available
Publicly Funded
Addenda Available
Post-Bid
Privately Funded
Bidding Soon
Documents Available
Publicly Funded
Addenda Available
Post-Bid
Privately Funded
Bidding Soon
Documents Available
Publicly Funded
Addenda Available
Post-Bid
Privately Funded
Bidding Soon
Documents Available
Publicly Funded
Addenda Available
Post-Bid
Privately Funded
Bidding Soon
Documents Available
Publicly Funded
Addenda Available
Post-Bid
Privately Funded
Bidding Soon
Documents Available
Publicly Funded
Addenda Available
Post-Bid
Privately Funded
Bidding Soon
Documents Available
Publicly Funded
Addenda Available
Post-Bid
Privately Funded
Bidding Soon
Documents Available
Publicly Funded
Addenda Available
Post-Bid
Privately Funded
Bidding Soon
Documents Available
Publicly Funded
Addenda Available
Post-Bid
Privately Funded
Bidding Soon
Documents Available
Publicly Funded
Addenda Available
Post-Bid
Privately Funded
Bidding Soon
Documents Available
Publicly Funded
Addenda Available
Post-Bid
Privately Funded
Bidding Soon
Documents Available
Publicly Funded
Addenda Available
Post-Bid
Privately Funded
Bidding Soon
Documents Available
Publicly Funded
Addenda Available
Post-Bid
Privately Funded
Bidding Soon
Documents Available
Publicly Funded
Addenda Available
Post-Bid
Privately Funded
Bidding Soon
Documents Available
Publicly Funded
Addenda Available
Post-Bid
Privately Funded
Bidding Soon
Documents Available
Publicly Funded
Addenda Available
Post-Bid
Privately Funded
Bidding Soon
Documents Available
Publicly Funded
Addenda Available
Post-Bid
Privately Funded
Bidding Soon
Documents Available
Publicly Funded
Addenda Available
Post-Bid
Privately Funded
Bidding Soon
Documents Available
Publicly Funded
Addenda Available
Post-Bid
Privately Funded
Bidding Soon
Documents Available
Publicly Funded
Addenda Available
Post-Bid
Privately Funded
Bidding Soon
Documents Available
Publicly Funded
Addenda Available
Post-Bid
Privately Funded
Bidding Soon
Documents Available
Publicly Funded
Addenda Available
Post-Bid
Privately Funded
Bidding Soon
Documents Available
Publicly Funded
Addenda Available
Post-Bid
Privately Funded
Bidding Soon
Documents Available
Publicly Funded
Addenda Available
Post-Bid
Privately Funded
Bidding Soon
Documents Available
Publicly Funded
Addenda Available
Post-Bid
Privately Funded
Bidding Soon
Documents Available
Publicly Funded
Addenda Available
Post-Bid
Privately Funded
Bidding Soon
Documents Available
Publicly Funded
Addenda Available
Post-Bid
Privately Funded
Bidding Soon
Documents Available
Publicly Funded
Addenda Available
Post-Bid
Privately Funded
Bidding Soon
Documents Available
Publicly Funded
Addenda Available
Post-Bid
Privately Funded
Bidding Soon
Documents Available
Publicly Funded
Addenda Available
Post-Bid
Privately Funded
Bidding Soon
Documents Available
Publicly Funded
Addenda Available
Post-Bid
Privately Funded
Bidding Soon
Documents Available
Publicly Funded
Addenda Available
Post-Bid
Privately Funded
Bidding Soon
Documents Available
Publicly Funded
Addenda Available
Post-Bid
Privately Funded
Bidding Soon
Documents Available
Publicly Funded
Addenda Available
Post-Bid
Privately Funded
Bidding Soon
Documents Available
Publicly Funded
Addenda Available
Post-Bid
Win the Right Construction Jobs to Fuel Your Success
-
Save time tracking down project leads.
Quickly find commercial construction jobs bidding in your area—complete with plans, specs, bidders list, and up-to-date project details.
-
Focus on the right projects for your business.
Filter searches by trade, location, building use, bidding status, keywords, and more.
-
Receive more invitations to bid (ITBs).
Get promoted to general contractors bidding out private projects for your trades in your backyard.
-
Keep your project pipeline full.
Build relationships with general contractors, owners, developers, and architects with access to complete contact details.
-
Submit winning bids.
Perform fast, precise material takeoffs and build accurate estimates with integrated digital takeoff and estimating tools including On-Screen Takeoff, PlanSwift, and QuoteSoft.